One Step to Change Food Safety Culture
14 Jun 2024
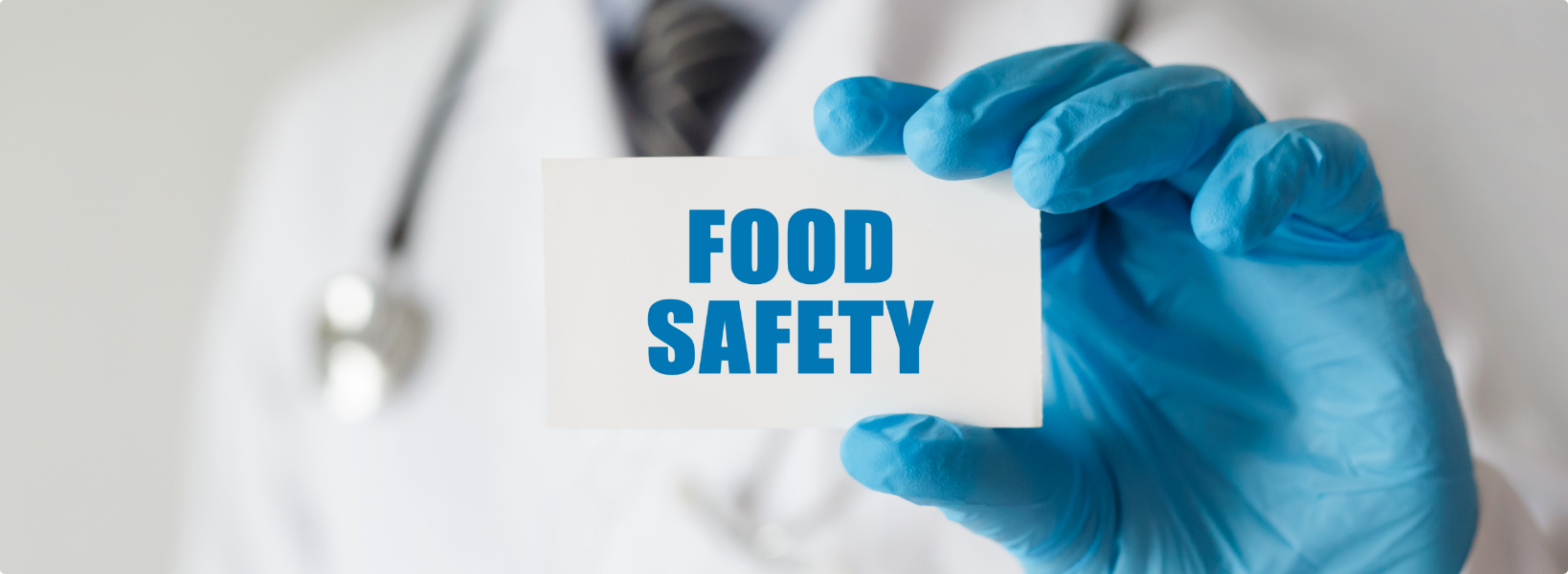
One Step to Change Food Safety Culture
Nobody likes crisis but it happens. And when it does, it presents an opportunity to improve the way we manage food safety. Let’s get started on a path to a simple solid system that makes sense to everyone.
In the counter-productive cycle we referenced in our previous post much focus is given to technical gaps; those gaps between compliance and standards. Most efforts to ‘improve the system’ have been overly focused on bridging those technical gaps. But here’s the issue; standards are not what makes food safe. Standards are a measuring tool, and often a rather crude one.
When it comes to food safety, we know so much depends on soft skills like interpretation, consistency of implementation and culture. These are not addressed in the standards but they are all-important and quite often the root of challenges we face in food manufacturing.
One of the most common soft gaps is the willingness to acknowledge a problem. In our experience, this is often the first gap that needs to be bridged when we work with a team on the ground in a plant. The old adage is true: “You can’t fix what you won’t acknowledge.”
We consistently encounter the same types of resistance that get in the way of acknowledging the truth of a situation:
- Breaking the status quo: “We’ve been doing it this way for years”
- Denial: “We’re already doing everything we can”
- Lack of faith: “Nobody can sustain the level of effort needed to be ready every day”
- Fear of the appearance of failure: “If it is so obvious, why didn’t I see it?”
Fortunately, the solution is simple; reframe the problem. If we rephrase the adage it can become “The first step to fixing a problem is to acknowledge it.” Create a path to success by embracing the real possibility of a positive cycle. I mean really embrace it! Pretty soon small problems get acknowledged and solved quickly before they become big problems.
Take for example spillage from the line. This is something we see tolerated quite often in a plant. There’s the perception spillage just happens and it’s not a problem.
Let’s reframe: Well if it’s liquid and it’s dripping on the floor, it eventually leads to wear and lifting on that same floor. Cracks appear and they get harder to clean. This becomes the perfect home for pests and bacteria growth. Now we have a problem.
Let’s reframe: Well if it’s liquid and it’s dripping on the floor, it eventually leads to wear and lifting on that same floor. Cracks appear and they get harder to clean. This becomes the perfect home for pests and bacteria growth. Now we have a problem.
Solution: Let’s acknowledge something needs to be done about spillage and fix it while it’s quite manageable and before it becomes a big problem. By doing this, we avoid unnecessary work like constant clean-up and the risk of pest infestation, bacteria growth, big repairs and maintenance expenses.
You've got an onsite mechanic who knows how to plug a hole in the conveyor belt, reposition equipment for good alignment or add depth to the sides of the conveyor where spillage is happening. The challenge is this work needs to be done during shutdown and once you’re in shutdown these repairs inevitably get dropped to the bottom of the list as a small problem. A little attention now prevents a big (and potentially costly) problem down the road.
And a new way of thinking introduces change. Be prepared; If you are going to look at the situation from a completely different perspective, you are going to see things differently. And that’s exciting because you’re ready to jump into a productive cycle of food safety.
So today, challenge your way of thinking and if you hear:
- “We’ve been doing it this way for years”
- “We’re already doing everything we can” or,
- “Nobody can sustain the level of effort needed to be ready every day”
Pause, reframe the problem as an opportunity to nip the issue in the bud, and look for a simple, effective solution.